KIMONO
Fashion tech designer: Laura Civetti
Photographer: Federica Ciccone
Model: Pauline Temme
Project develops during Fabricademy
course 2017/2018
The overproduction remains one of fashion’s costliest, transforming hundreds of acres of land into massive warehouses. Clearly, if a fashion industry lists more lines, the retailer will need to keep more inventory and the warehouse will normally run out of space due to rapid growth, seasonal peaks, or even a slow sales period. It is an admitted fact that the carrying of inventories involves an annual cost of approximately 25 % of the value of the inventory. Most of the success and failure of a business organization depends on the inventory maintenance, particularly the textile inventory.
Thus, What about if the fashion houses could reduce the inventory management stock and rethink at the textile production, tailoring up its on-demand fabric or smaller material selections based on features needs and production quantities. Therefore, shifting the textile material production from using external resources as suppliers into internally material production, it brings the design production to be no longer limited and acquiring unique freedom to start a new investigation to address specific design requirement, guiding in an unexpected solution, for an instance a complex shape or compound that could not massively be produced using limited material or toxic compound.
Kimono Bio-plastic dress aims to lower the barriers of fabrication and design toward creative freedom. By incorporating, in the textile material, behaviors, and capacity that were not found in supplier textiles. Thus I investigate the use of organic-inorganic hybrid material and how to optimized design production. This approach encouraged me in a more interactive design process that allowed me to tailored material behaviors with production needs, rising up the framework for conversations around material issues.
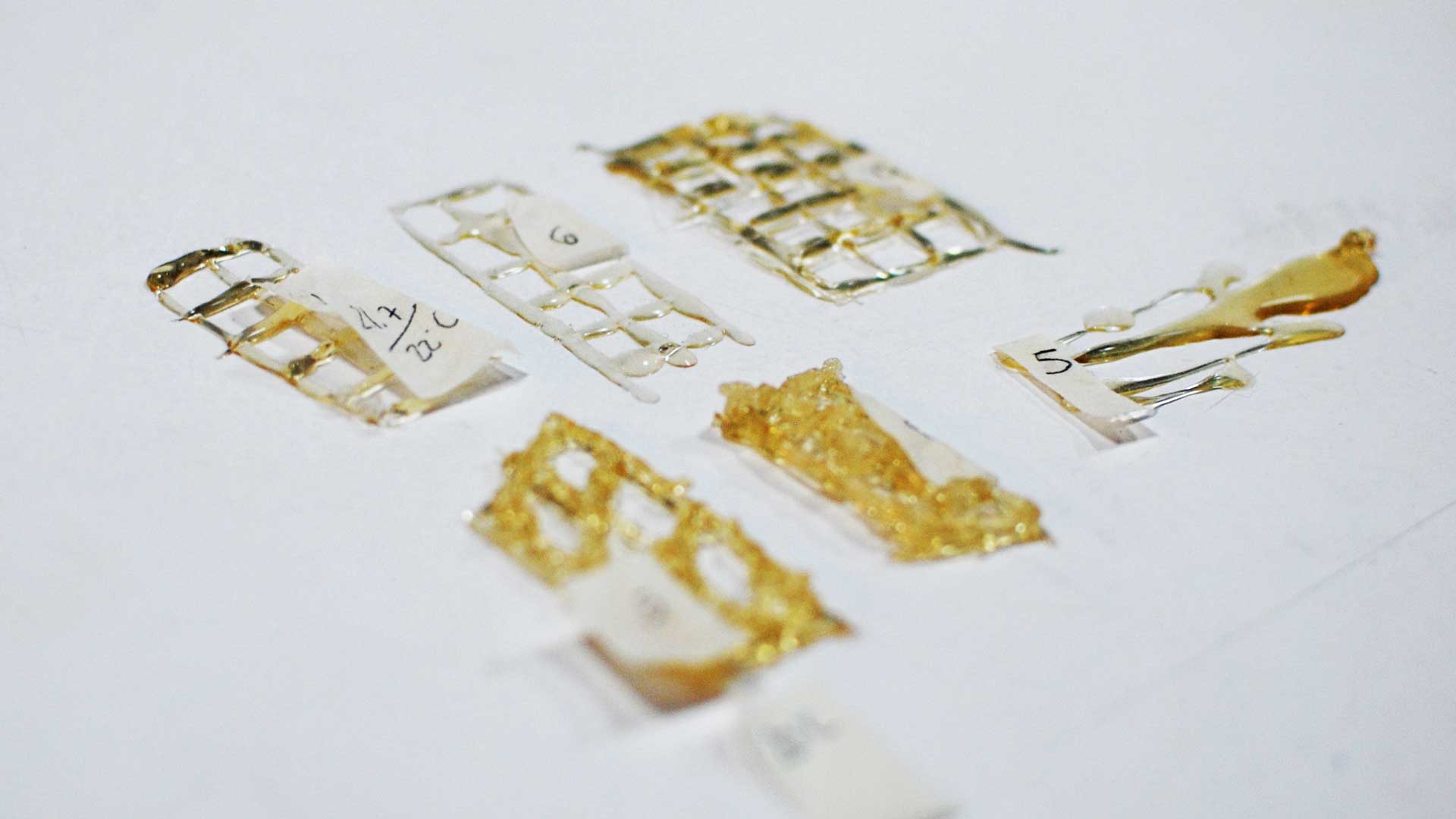
MATERIAL RESEARCH
STRUCTURED BIOPLASTIC
During the fabrication material process, it has been using the tulle as a material structure, in order to avoid material contraction during the drying process.
The tulle has been laid down on top of bioplastic, without submerging it on the liquid. That gave two textures at the material, ones rough and matt by the Tulle layer and others smooth and shiny by the mold. Note: Since tulle is a net, it traps the air. If the tulle is positioned first that the bioplastic, it will create bubbles during the pouring process.
DESIGN
MODULAR CONFIGURATION SYSTEM
Design digitally, the Kimono dress is a modular surface characterized by the variation of its piece according to the body location. Using parametric software was possible to control the model variables such as thickness and length to establish greater or lesser textile flexibility.
Additionally, the parametric systems allowed me to reconfigure all elements according to the material.
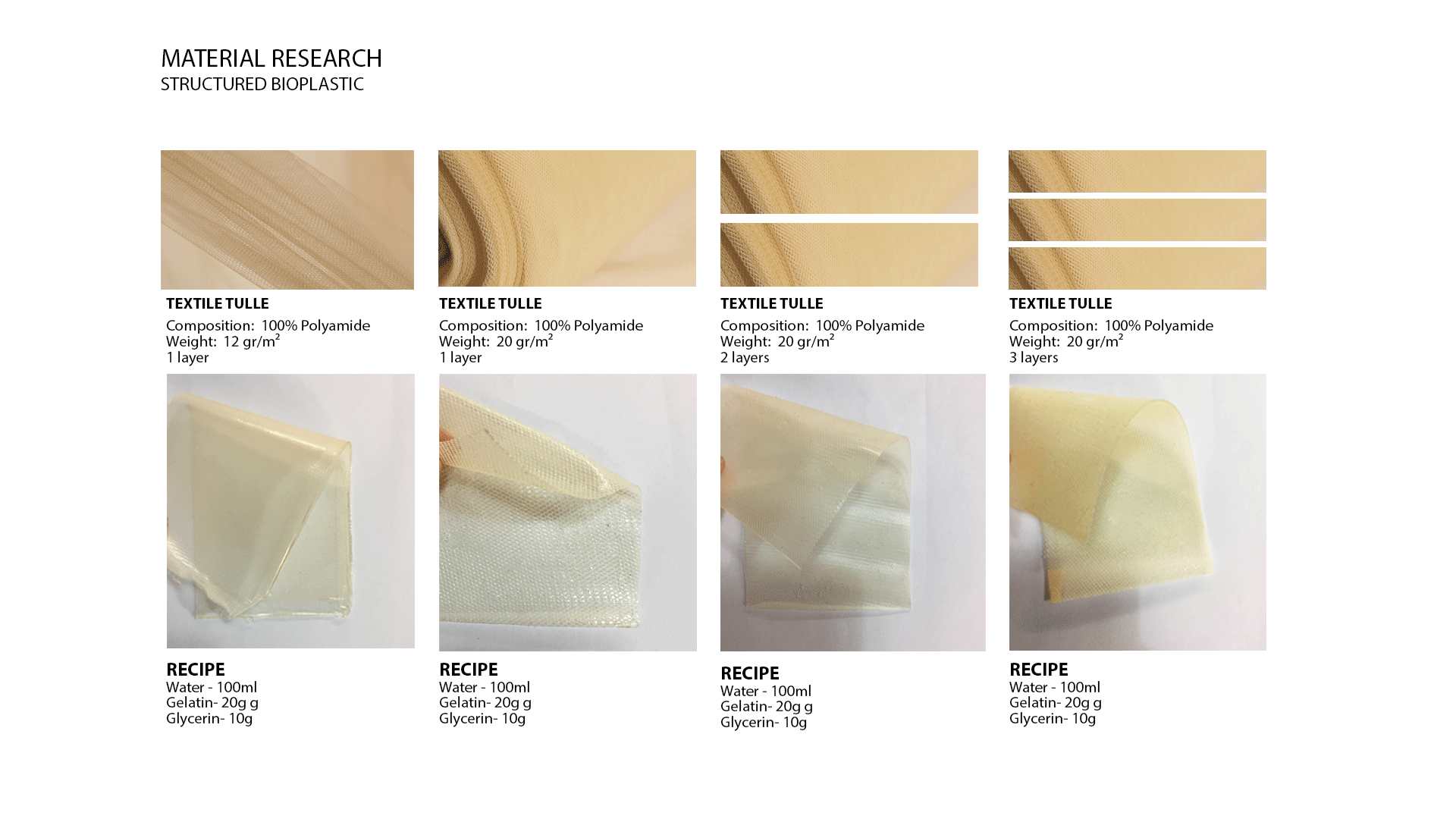
FABRICATION
To cut the modular piece from the customized material, I used a laser-cut machine. Against all the expectations, the material acted really well, in terms of the stretch, pulling, and resistance. Thanks to the burning edge made by laser-cut, the element was much stronger and resistant than other materials tested.
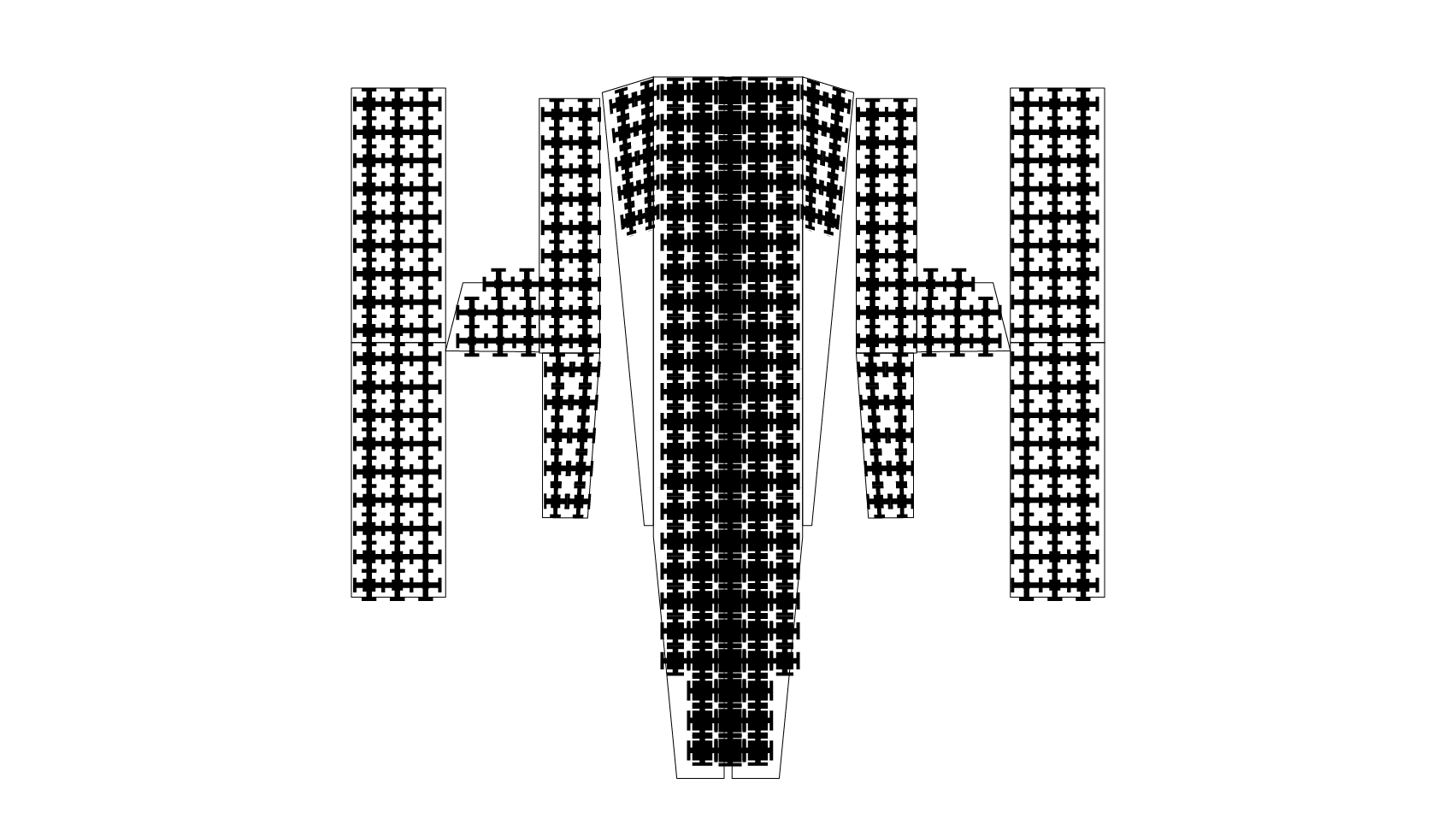
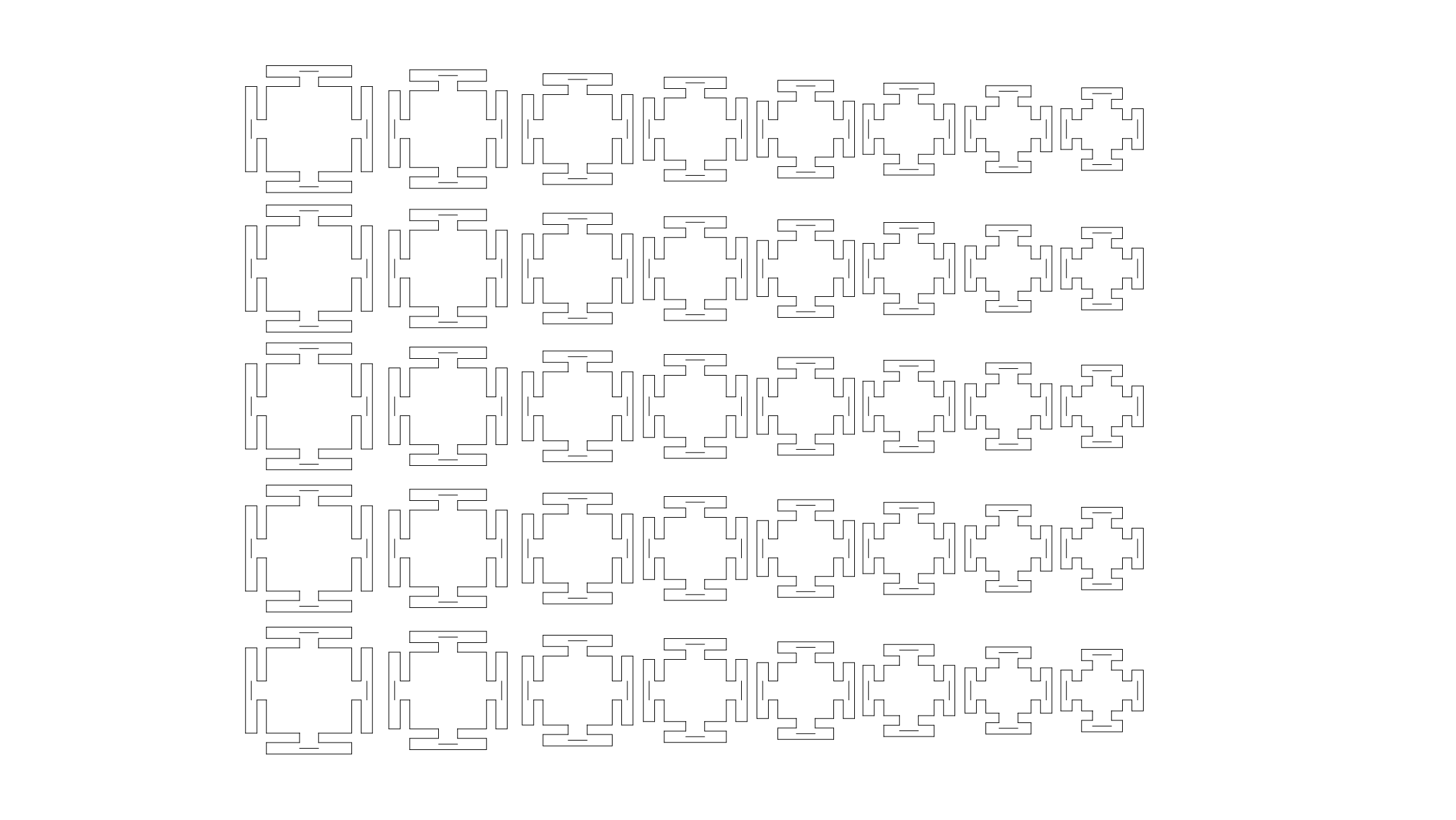
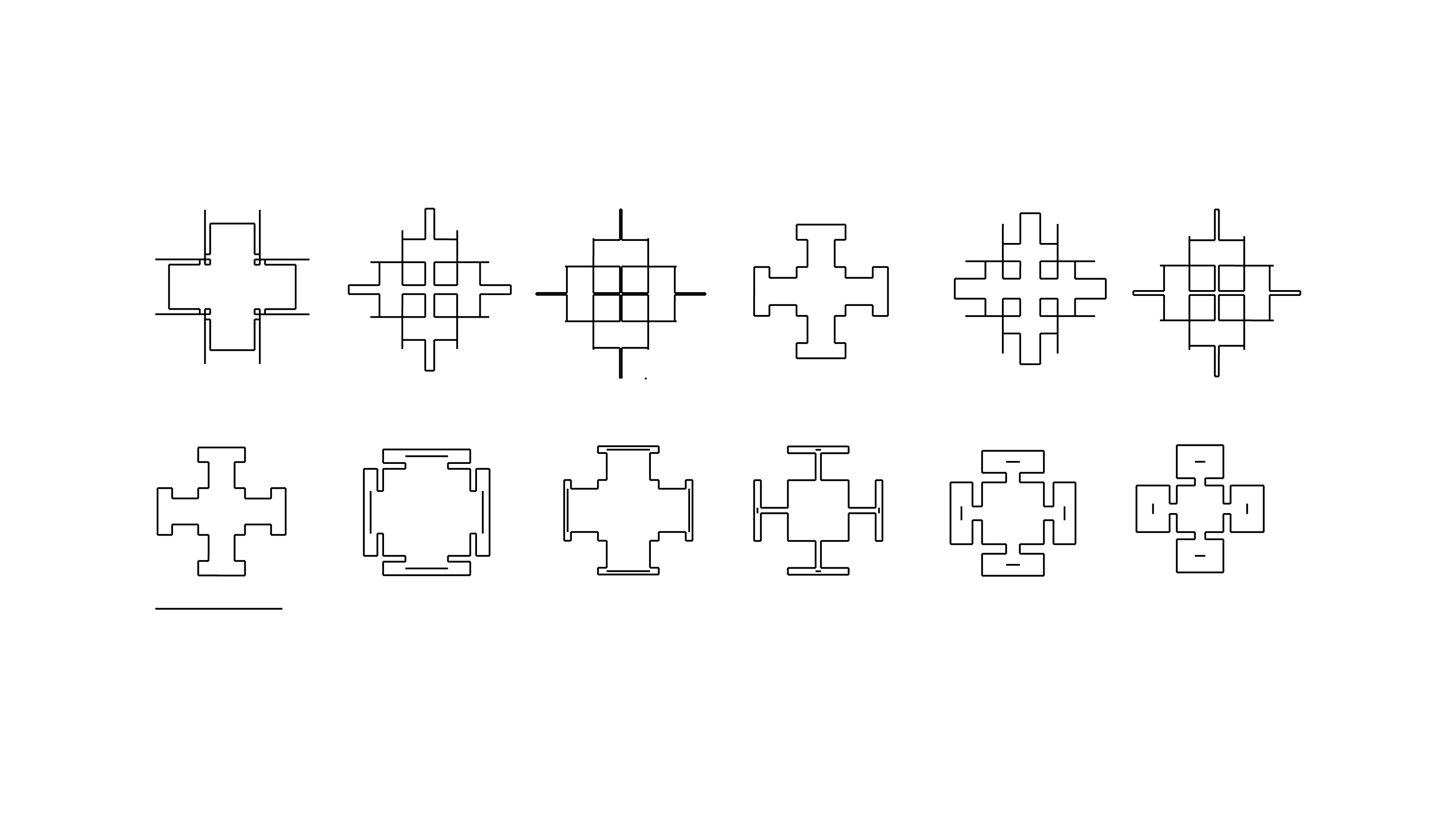
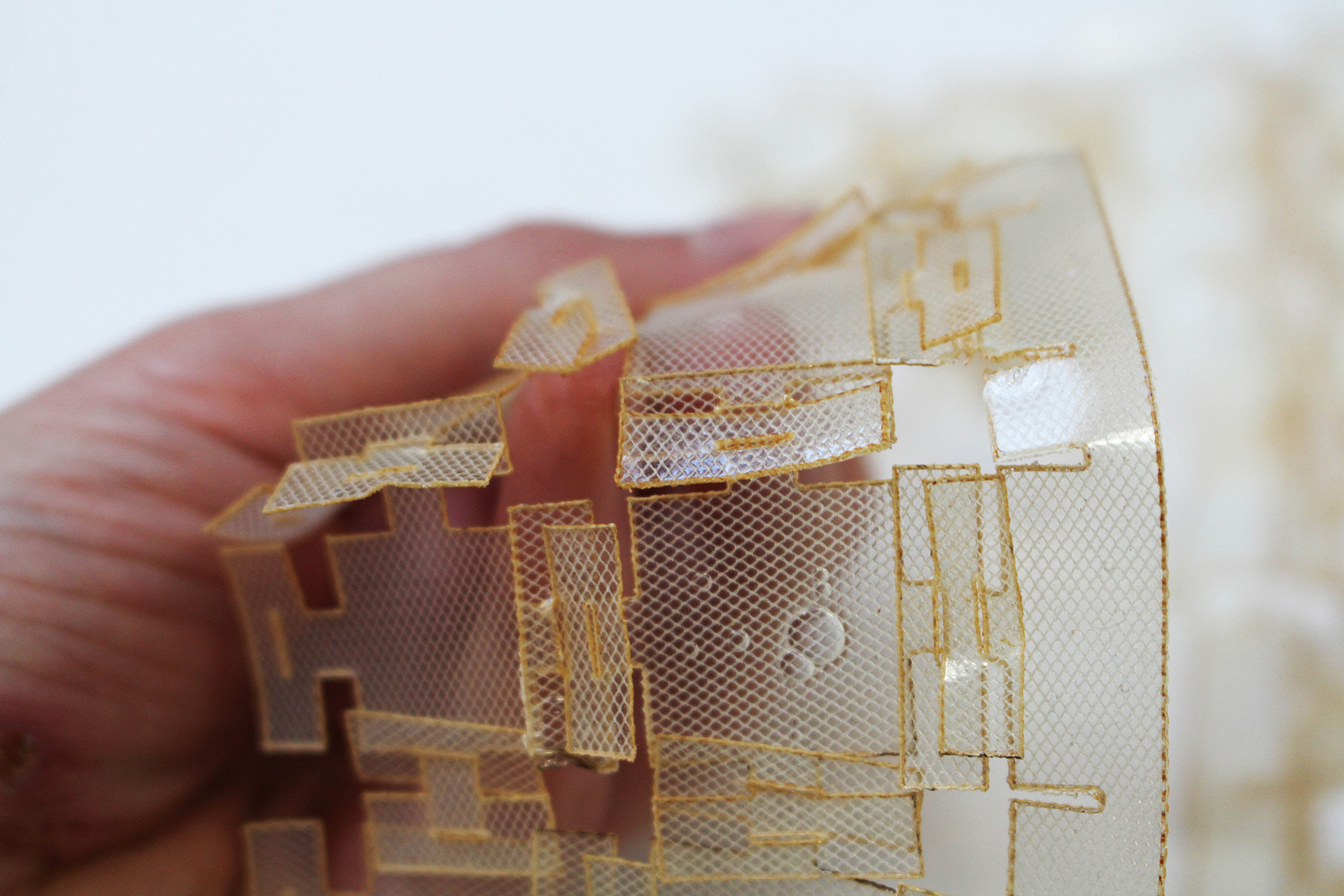
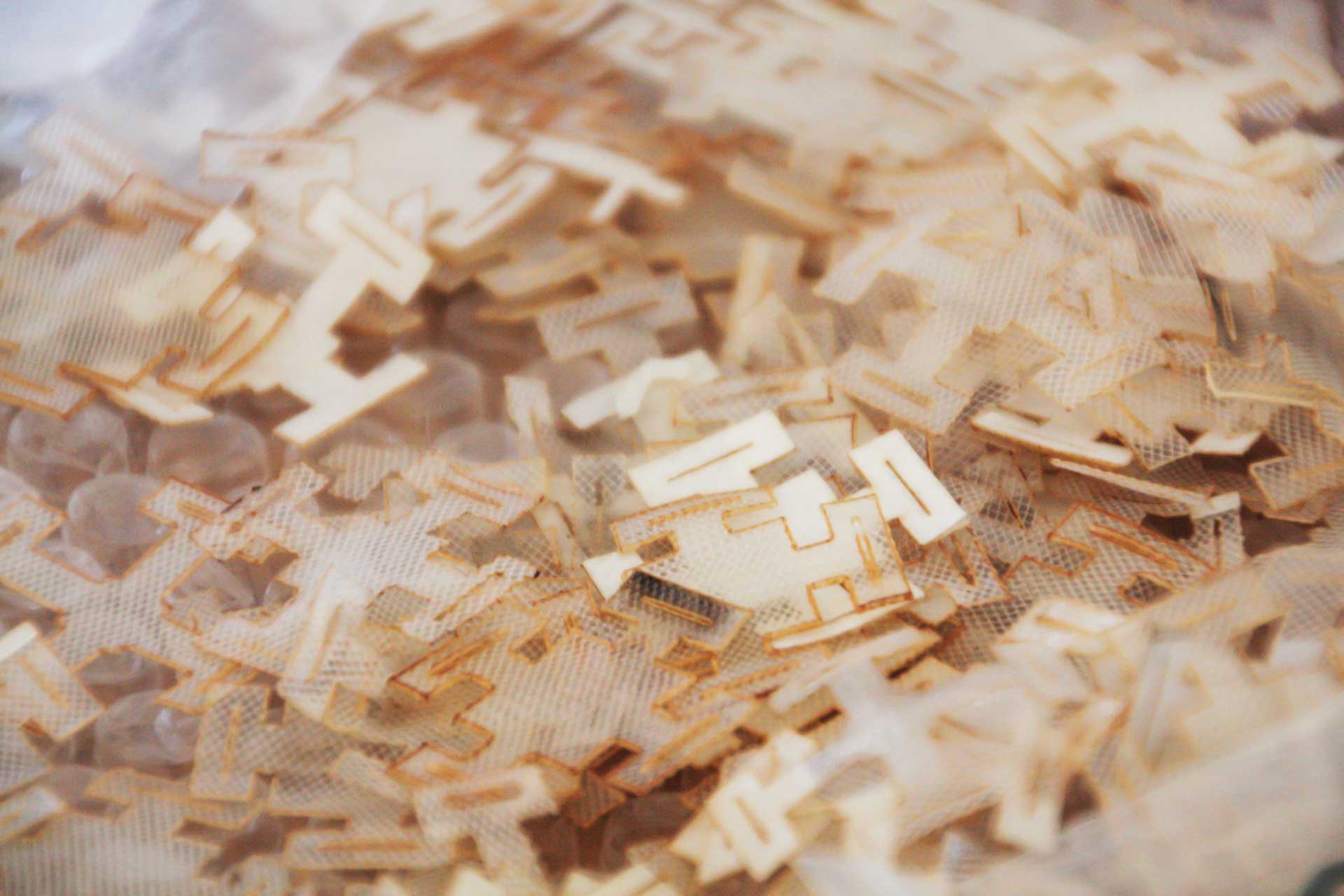
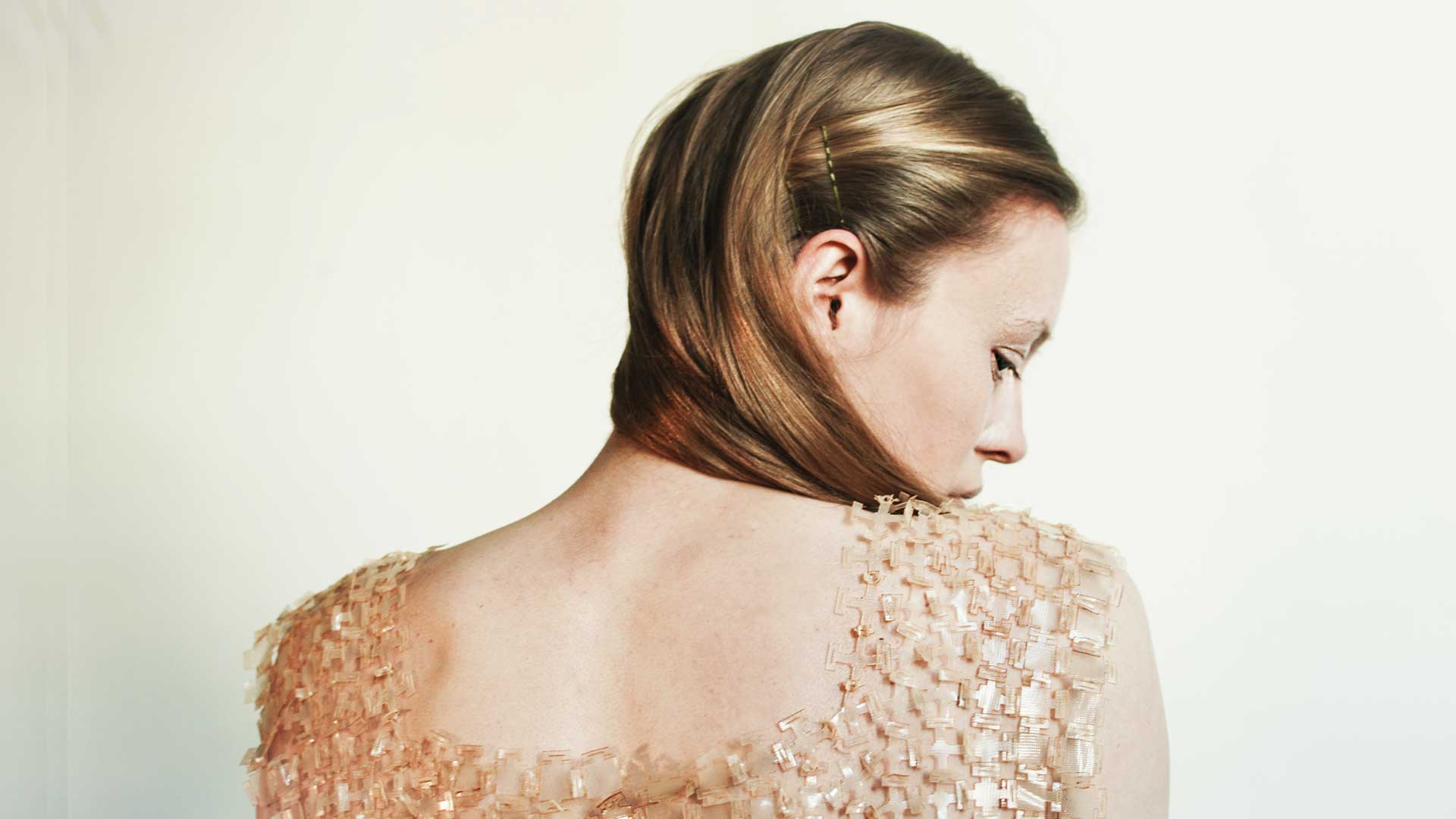
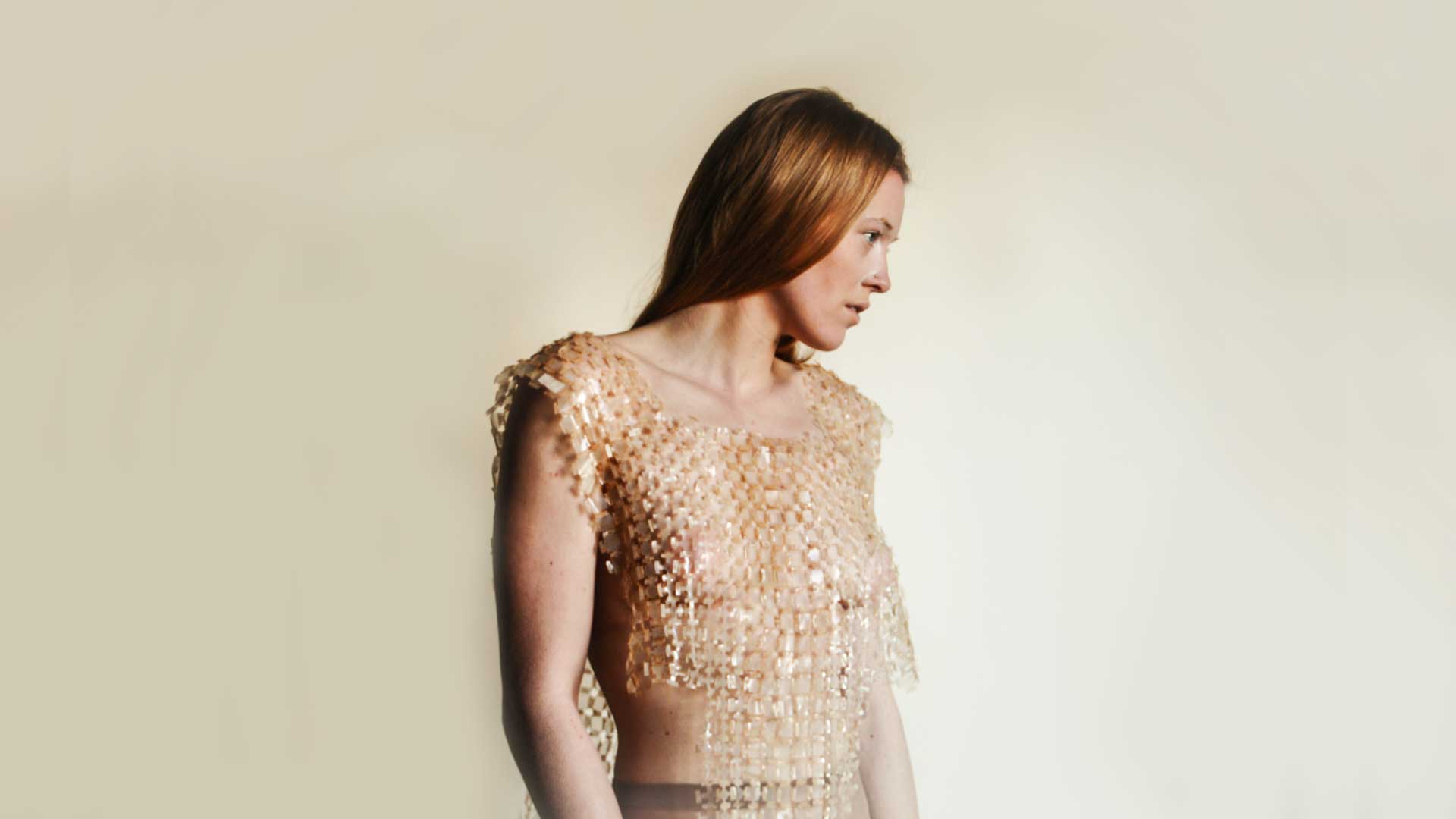
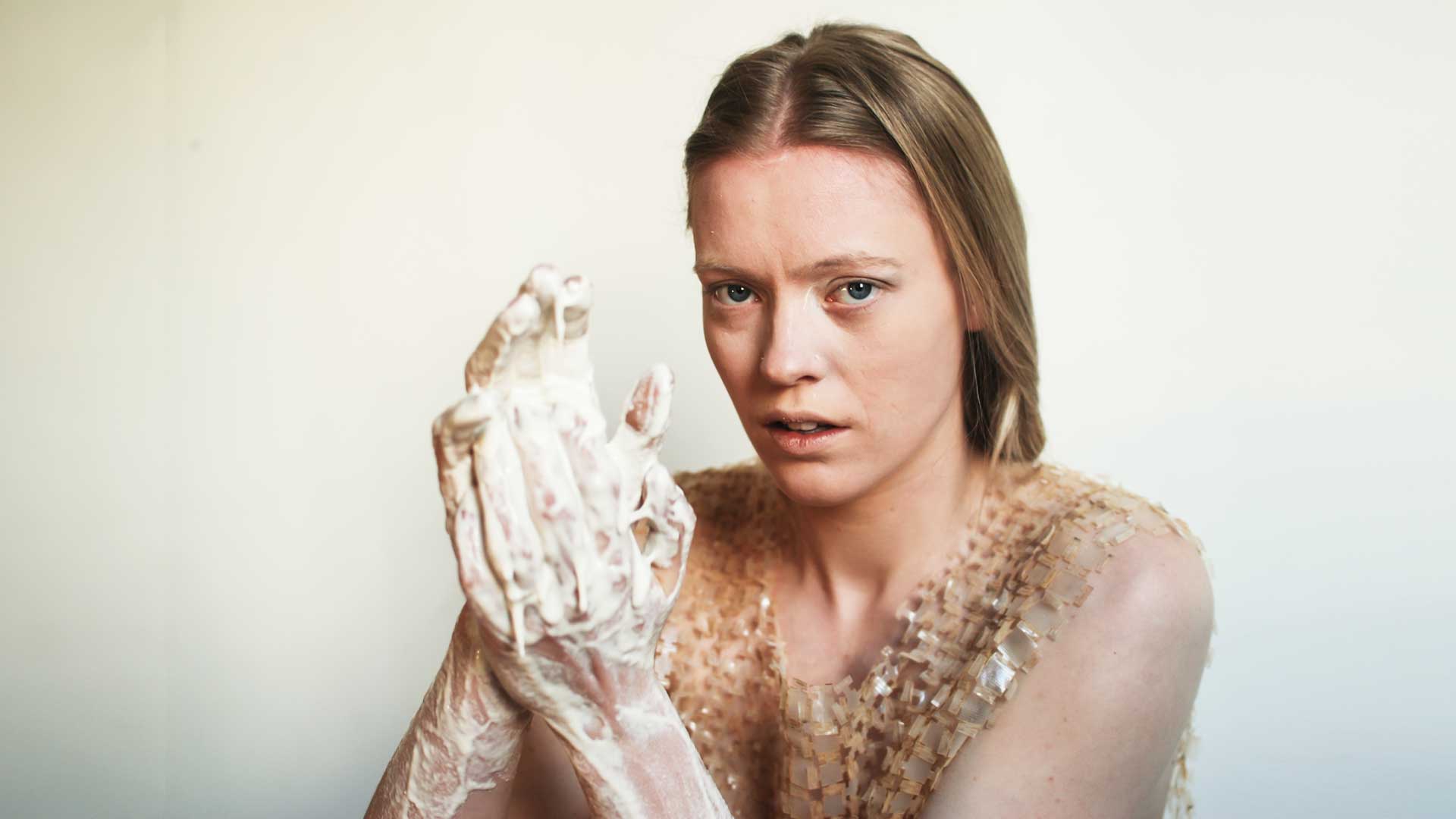